Think about what you are doing and why you are doing it.
I rarely comment on plastics because of the fact there are so many overnight experts and so much misled info available.
You people are H&S disaster areas but if you must play with pretty patterns then think before acting.
What is the application and aim????
If you are extruding surgical tubing then yes you must adhere strictly to the correct practices, sterilizing, preheating / cooking.
Moisture and air content is critical both can damage the over engineered machinery and or the patient and ruin any thermo setting plastics.
If you are forming, then preheating is only required for the creation of the form, both the material and former should be heated to the point where the material becomes flexible enough to create the form.
This only requires the temperature to be right regardless of the time taken to heat it, basically you are bending thermo formed plastic not roasting a Sunday joint.
You are doing neither of these you are using a chemically setting epoxy resin which is a different form of plastic altogether, do not confuse the issue and read the correct instructions which will come with the product.
Just because it is written on the web it doesn't mean it's correct.
A whole industry has sprung up over the last few decades of the diy kit probably started by the car repair (Halfords) thing of body fillers etc, people are taking dangerous and potentially lethal chemicals into their homes.
Resins are nothing new, Galleons were put together with cascamite which is the first (to my knowledge) resin mix.
Your application of these products is neither essential nor critical, what does it matter if it has a bubble of air or water in it?
Why does it have to set in 5 minutes instead of 5 hours?
What are the consequences of a ruined pour? Bin it and do another one.
Who are you harming? Everyone around you and yourself, read the H&S sheet that comes with the product.
The chemical reaction that occurs during the curing process of your product, generates enough heat to make a long preheating process irrelevant, in anything other than extreme temperature changes should answer your original question.
You will continue with this foolhardy experiment, so my tip for you is when mixing use an L shaped stirrer and stir under the liquid will produce no or less air bubbles.
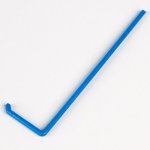