Well I made a start with the ebonite Zulutiming so kindly sent me. It's the first time I've worked with it and quite frankly I don't know what to make of it - it stinks of sulphur and burning rubber (since it is in fact sulphur-treated rubber that shouldn't have been a surprise) and spews out ribbons which choke the lathe in no time. It's also very heat-sensitive, which I learned by destroying the first component I made while trying to drill it (too fast). But on the upside it works really easily and seems to have quite a bit of strength.
First a shot of the ribbons:
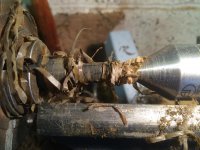
And a couple of the bulb filler skeleton:
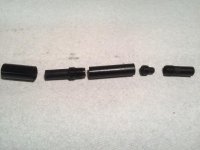
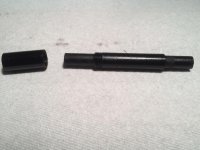
I'm used to making these with brass, so there's a bit of learning still to do as I skin it with timber. More as it happens.
First a shot of the ribbons:
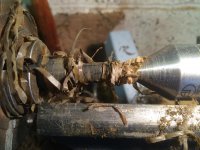
And a couple of the bulb filler skeleton:
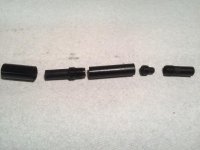
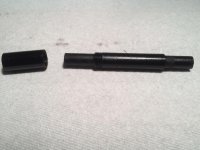
I'm used to making these with brass, so there's a bit of learning still to do as I skin it with timber. More as it happens.