George Watkins
Registered
hello folks
here are some quick camera phone pics of an oak vessel being turned earlier today.
I had cut the blank from a much larger log a few days earlier, i start it between centers, its approx 6" by 14"
Mounted onto a faceplate now, I find knots at both ends which I want to avoid
I remove a couple of inches to get rid of the upper knot
the vessel starts to take shape, i stop at this point and hollow down to final wall thickness to about 2/3rds of the overall depth
a bit of winter sun!
hollowing in progress, I want a 1/4" wall thickness as i am to carve the piece once it has dried.
tools of the trade
once i had hollowed the inside to 2/3rds I go back to the exterior and remove the waste wood which was adding strength during hollowing and shape the bottom 1/3rd, then i go back inside and finish the hollowing.
all hollowed out and ready to sand
the finished vessel
here are some quick camera phone pics of an oak vessel being turned earlier today.
I had cut the blank from a much larger log a few days earlier, i start it between centers, its approx 6" by 14"
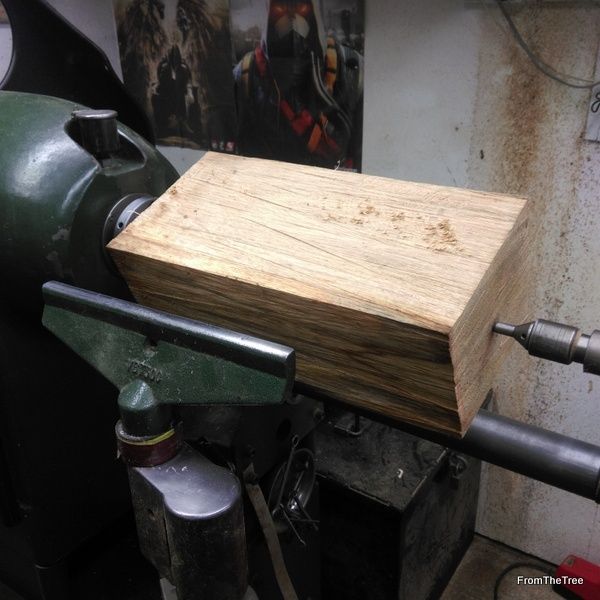
Mounted onto a faceplate now, I find knots at both ends which I want to avoid
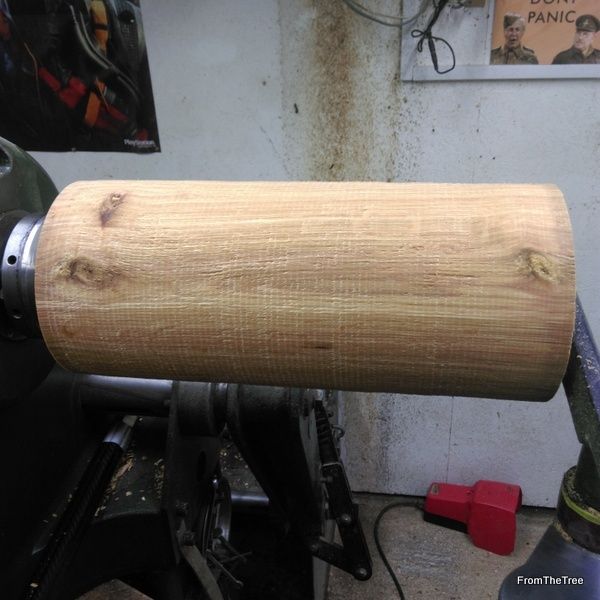
I remove a couple of inches to get rid of the upper knot
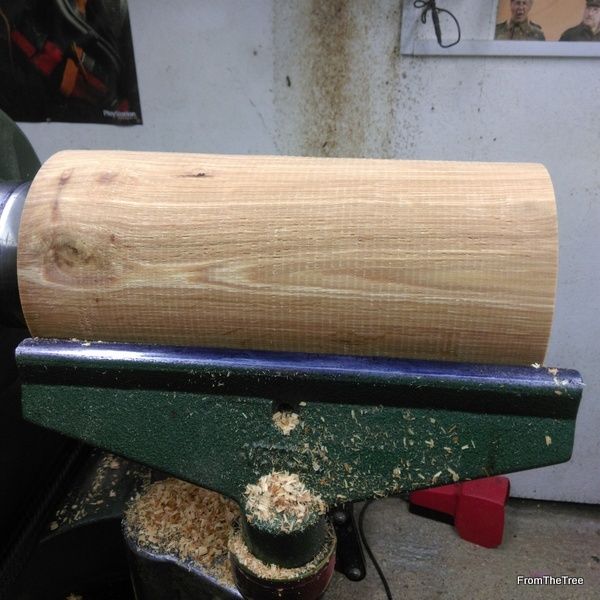
the vessel starts to take shape, i stop at this point and hollow down to final wall thickness to about 2/3rds of the overall depth
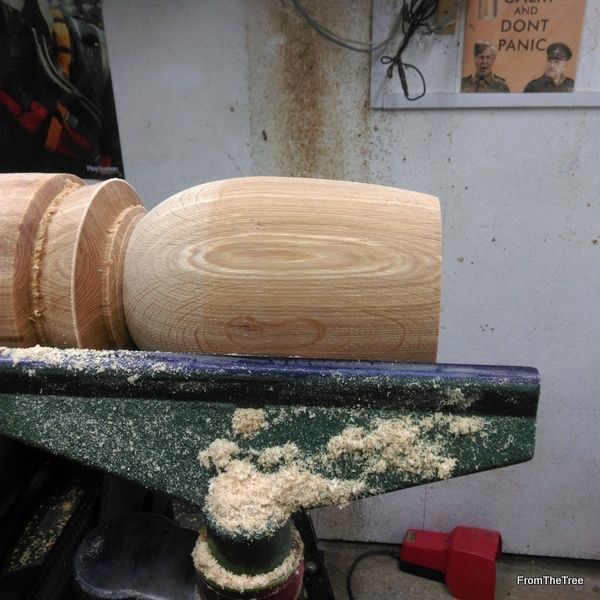
a bit of winter sun!
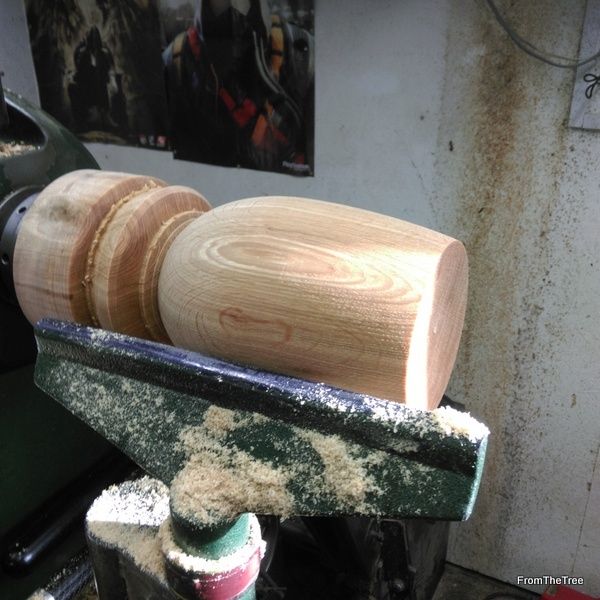
hollowing in progress, I want a 1/4" wall thickness as i am to carve the piece once it has dried.
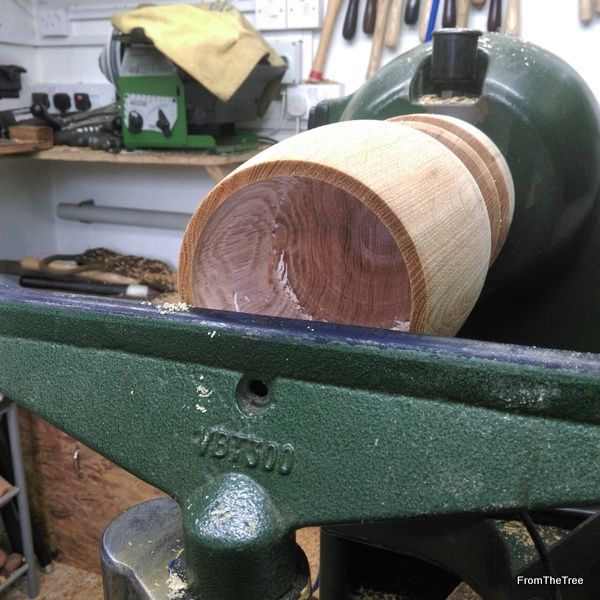
tools of the trade
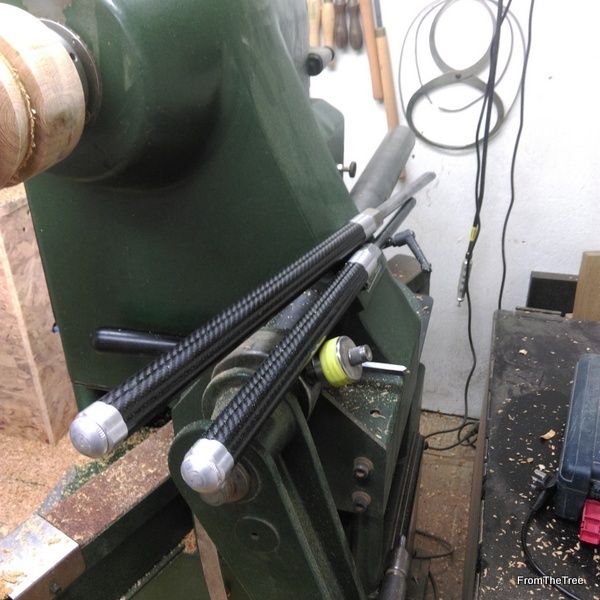
once i had hollowed the inside to 2/3rds I go back to the exterior and remove the waste wood which was adding strength during hollowing and shape the bottom 1/3rd, then i go back inside and finish the hollowing.
all hollowed out and ready to sand
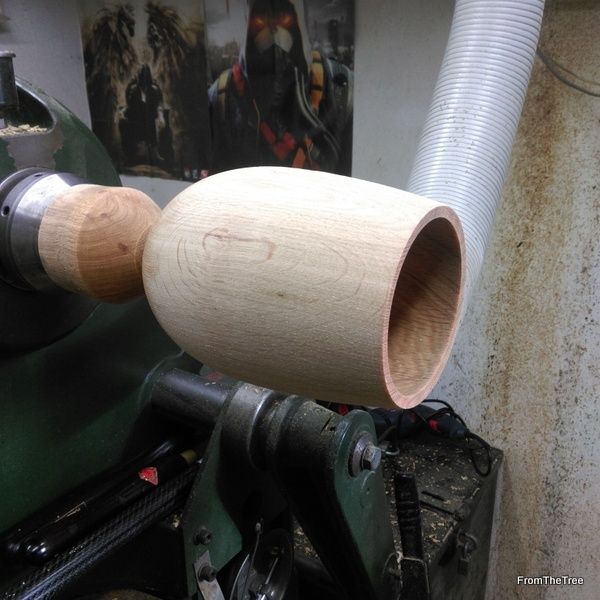
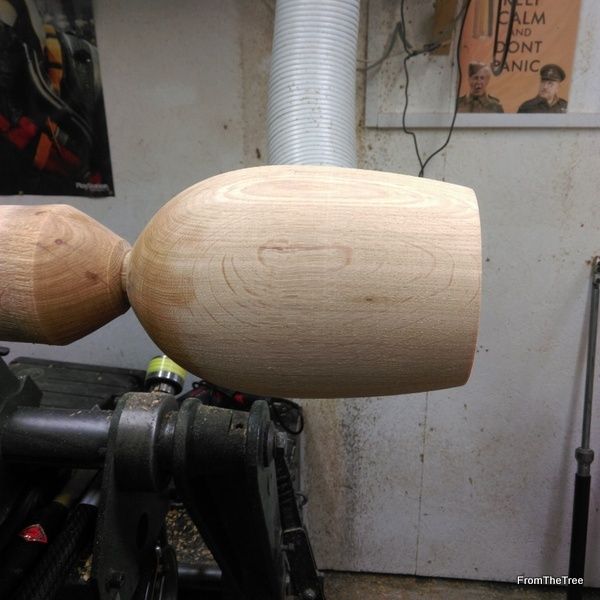
the finished vessel
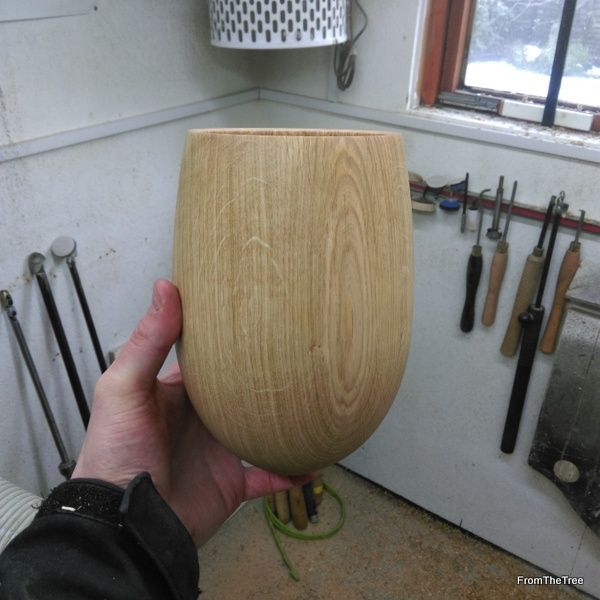