Bob Ellis
Graduate Member
I like the smoothness and shine I get using a CA finish, but I am having a problem when it comes to removing the blanks from the mandrel because the CA glues them to the bushes. I have tried snapping them off and I have tried using a parting tool to cut through the CA that builds up on the bushes. Whichever method I use, when I smooth off the ends of the blanks by gently rubbing them in a circular motion on fine abrasive paper laid flat on my work table, either a small piece of the finish breaks off or, more frequently lifts a bit so that the finish becomes milky (see the cap end of the photo below).
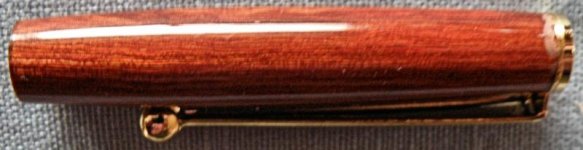
The white line along the pen cap is not a blemish - it is a reflection off the finish. The fault is next to the cap finial.
I saw a Barry Goss video in which he advised applying a small amount of CA carefully to each end of the blanks after removing them from the mandrel to stop the CA finish from lifting or breaking loose when the ends are smoothed down. This seemed to make sense, so I tried it on my latest pen (the one in the photo). It worked well on three of the ends, but part of the finish lifted on the cap end of one of the blanks, so I will have to either find a way of repairing it or take the finish off that blank and start again.
Any ideas of how I can overcome this problem? I have tried other finishes, but I prefer CA and want to make this method work more consistently for me.
Since it might be relevant, here is a summary of the way I apply the CA finish. Having shaped them, I smooth off the blanks using Micromesh pads down to at least 4000 grit. Then I clean them with acetone and leave them to dry for a few minutes. I apply a dozen coats of thin CA glue using small pieces of kitchen roll and spraying with accelerator between each coat. After leaving this to harden for about an hour, I use Micromesh 1500 to smooth out irregularities in the CA finish and then stop the lathe and work laterally along each blank until all shiny bits have been removed, which ensures that the surface is completely smooth. Then I take the Micromesh all the way up to 12000 grit until the finish is very shiny and finally I polish the blanks with Silvo. Thus far everything works perfectly.
The problem comes when I remove the blanks from the mandrel. The CA sticks the bushes to the ends of the blanks. I have tried snapping them loose and I have tried using a parting tool against the bushes to break through the CA. Both methods leave some CA proud of the end of the blanks. As I mentioned earlier, I rub the ends gently in a circular motion on a piece of fine abrasive laid flat on my work table to smooth them off. More often than not this works, but sometimes it just appears to do so and when I assemble the pen I end up with the situation in the photo, which means that I have to disassemble it. Since I don't know of any way of repairing the finish, I have to spend time removing the entire CA finish down to the wood and reapplying it.
I shall hold off trying to repair this pen until I hear from some of the wise and experienced turners who offer their advice so generously on this great forum.
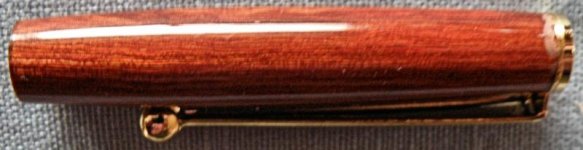
The white line along the pen cap is not a blemish - it is a reflection off the finish. The fault is next to the cap finial.
I saw a Barry Goss video in which he advised applying a small amount of CA carefully to each end of the blanks after removing them from the mandrel to stop the CA finish from lifting or breaking loose when the ends are smoothed down. This seemed to make sense, so I tried it on my latest pen (the one in the photo). It worked well on three of the ends, but part of the finish lifted on the cap end of one of the blanks, so I will have to either find a way of repairing it or take the finish off that blank and start again.
Any ideas of how I can overcome this problem? I have tried other finishes, but I prefer CA and want to make this method work more consistently for me.
Since it might be relevant, here is a summary of the way I apply the CA finish. Having shaped them, I smooth off the blanks using Micromesh pads down to at least 4000 grit. Then I clean them with acetone and leave them to dry for a few minutes. I apply a dozen coats of thin CA glue using small pieces of kitchen roll and spraying with accelerator between each coat. After leaving this to harden for about an hour, I use Micromesh 1500 to smooth out irregularities in the CA finish and then stop the lathe and work laterally along each blank until all shiny bits have been removed, which ensures that the surface is completely smooth. Then I take the Micromesh all the way up to 12000 grit until the finish is very shiny and finally I polish the blanks with Silvo. Thus far everything works perfectly.
The problem comes when I remove the blanks from the mandrel. The CA sticks the bushes to the ends of the blanks. I have tried snapping them loose and I have tried using a parting tool against the bushes to break through the CA. Both methods leave some CA proud of the end of the blanks. As I mentioned earlier, I rub the ends gently in a circular motion on a piece of fine abrasive laid flat on my work table to smooth them off. More often than not this works, but sometimes it just appears to do so and when I assemble the pen I end up with the situation in the photo, which means that I have to disassemble it. Since I don't know of any way of repairing the finish, I have to spend time removing the entire CA finish down to the wood and reapplying it.
I shall hold off trying to repair this pen until I hear from some of the wise and experienced turners who offer their advice so generously on this great forum.